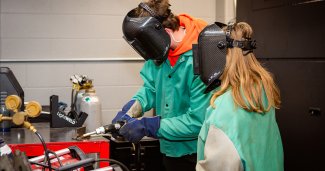
In the new Don Wood Foundation Advanced Metal Technology Lab, ONU mechanical engineering students are exploring ways the cutting-edge systems can enhance outcomes for capstone projects, competition teams, class assignments—and, their future employers.
“Our students are excited and eager to learn the capabilities of the new equipment,” said David Mikesell, Ph.D., professor of mechanical engineering.
The lab, which opened in the fall, was funded through a $1.05 million grant from the Don Wood Foundation, a private Fort Wayne foundation dedicated to the advancement of manufacturing, entrepreneurship, leadership, and related education in the Midwest.
The lab is outfitted with an Amada industrial laser capable of cutting up to an ½ inch thick plate of any metal; a Markforged Metal X 3D printer, which includes a wash tank and sintering oven; and an IPG Photonics laser welder.
According to Mikesell, the laser welder is an emerging technology, and ONU is fortunate to own one of only a few in Ohio.
“A lot of industries don’t know it exists yet; it’s still in its infancy,” he said. “So, there is a real opportunity for our graduates to be able to educate their future employers on the laser welder and be an asset with their knowledge.”
Traditional methods of welding, he explains, require a high-level of skill. “With the laser welder you can get an amazing quality weld with very little skill,” he explained. “It’s almost like magic.”
The industrial laser is another valuable new tool in the lab, providing advantages to capstone and competition teams. When it comes to cutting metal, the laser “is arguably the best tool for the job,” said Mikesell, because it provides accuracy and quality at a low operating cost.
Previously, teams requiring laser-cut items had to outsource the work, but now they can complete the work in-house for a fraction of the cost.
The lab’s 3D metal printer is also an essential tool for students to master, said Mikesell, because the tool’s use in manufacturing is growing exponentially.
Mikesell recently met with engineers at the Ford Motor Co. Sharonville (OH) Transmission plant. They demonstrated how 3D metal printers “have totally revolutionized the way they repair machines and make spare parts and replacement parts for their machines” while providing tremendous cost savings
Ben Eiden, a mechanical engineering student and project manager for the ONU SAE Baja team, says his team is most enthused about Metal X 3D printing system. They’ve already utilized it to manufacture u-joint yokes and wheel hubs for their off-road vehicle entry.
“Most of these parts were previously made by other shops with long lead times, so having the ability to make them in house allows us to iterate and fine tune every component. It will definitely give us a competitive edge when racing wheel to wheel with other teams.”
Learning the ins and outs of these manufacturing systems will also aid him in his future career, he says.
“This new equipment has shown me just how advanced 3D printing has become. My experience using the Metal X will be very useful in the manufacturing field as I determine the most cost effective and efficient ways to produce products.”