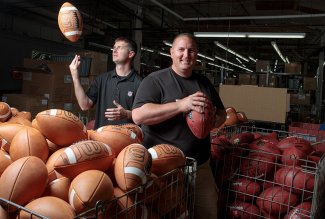
This article originally appeared in the Summer 2019 issue of ONU Magazine
When a company hangs its hat on making something that hasn’t changed in more than 75 years, innovation is not the first word that comes to mind. But in the case of the Wilson Football Factory in Ada, Ohio, maybe it should be.
The leather footballs manufactured there are special to American sports history. Wilson is the only game ball supplier the National Football League (NFL) has ever had and therefore every point ever scored in an NFL game has been with a Wilson football. Since 1955, those points were scored with footballs made in Ada.
That long history is sacred to the NFL, and as such, every effort has been made over the years to ensure that the records and statistics from previous eras of football remain pristine. While there have been rule changes that impact the way the game is played, Wilson and the NFL have kept the football —the one thing required for every offensive statistic— unchanged. Until recently that is.
In 2015, Mike Springer, BS ’99, a process/manufacturing engineer at Wilson Sporting Goods, was part of the small team that the NFL asked to do something that had never been done before. They asked them to change “The Duke.”
The Duke is the nickname of the NFL game ball. It is the crown jewel of Wilson’s product line, and it is so specialized that it still made by hand. Even the leather is highly scrutinized. Though commonly referred to as a pigskin, a football is actually cowhide, and the leather is procured from the same supplier in Chicago that provides Louis Vitton with the leather for its high-end luxury purses and bags.
The change Springer was tasked with making was in both materials and the manufacturing process. In 2014, a company named Zebra partnered with the NFL to begin tracking players’ movements during games. Two RFID chips in the players shoulder pads relayed information to a series of receivers mounted to the top of the teams’ stadia. When interpreted through computer programs, the player on the field became a dot on the screen. This initial foray into individual player data collection provided the NFL with the first of its Next Gen Stats, which show fans the speed of players, the amount of ground covered during a game, and where and when a player moved on the field. For fans, it’s fun to see how fast their favorite player can run, and for coaches and team personnel, it can show them how accurately their players play compared to how the play is intended to be run. But without the ball being represented in the data as well, the picture was incomplete.
That’s when Zebra provided Wilson with a small 3.2-gram electronic sensor and a simple request — stick it in the Duke. For Wilson, this was easier said than done. NFL quarterbacks rely on feel, and they have an uncanny ability to notice irregularities. Essentially, Wilson had two jobs: Put the sensor in the ball, and make it impossible to detect.
“This is the first big change in the NFL ball ever,” says Springer.
Springer helped devise the plan to weld the sensor into the pvc air bladder directly beneath the NFL shield logo on the Duke. This solved their quarterback problem as most players naturally avoid gripping the logo, and it worked structurally because it was protected from the most intense impacts the ball endures (kicking and punting), which happen on the bottom of the ball.
For the NFL’s Next Gen Stats, adding a sensor in the ball was the final piece in putting together a complete digital representation of an NFL game. By 2018, the Zebra system was available for use for every game. All 30 stadiums, along with Wembley Stadium in London, England, and Estadio Azteca in Mexico City, Mexico, were outfitted with the technology. Every one of the 24,960 footballs Wilson provided the NFL had sensors in them. The era of analytics had arrived.
“Now there are sensors not only in the shoulder pads and in the footballs, but all referees and umpires have sensors on them as well. And they even have sensors in the end zone pylons, the field goal posts and the chain gangs on the sideline. There are sensors all over the field,” says Springer.
The analytics generated by the Zebra/NFL partnership are fueling innovation on the field, and entertainment off of it. Now that the curtain has been peeled back from what big data can contribute to the NFL, Wilson is interested in seeing how far a smart football can go.
In addition to supplying NFL game balls, Wilson is also a major supplier of leather footballs to NCAA, high school and youth leagues. In these developmental environments, Wilson envisioned an opportunity to use data to help players get better, rather than just document performance. With that idea in mind, the Wilson X-Pro Connected Training System was born.
The X-Pro is a technology upgrade that Wilson can manufacture into any of their high-end leather footballs. It too comprises an in-ball sensor and accompanying software to record and interpret data. However, unlike Zebra, the X-Pro collects information pertaining to the mechanics of a football in flight rather than tracking its position on the field. Wilson’s sensor measures spin rate and spiral efficiency, release time, launch angle, velocity and throw count. Once the data is interpreted and visualized into charts and graphs, the X-Pro system offers deep, yet accessible, insights into a quarterback’s performance.
According to Daniel Hare, senior engineer for Wilson’s Advanced Innovation team, new uses for the data the X-Pro delivers are being discovered all the time.
“A lot of teams are interested in learning about the time it takes the ball to reach the quarterback in a shotgun snap. That’s not necessarily something we envisioned when we started developing the technology,” says Hare. “Another really important use for the system is using it to assess players recovery from injury. If a quarterback is rehabbing, a team can look at the rehab data and compare it to pre-injury data to see how close he is to 100 percent. Obviously, comparing multiple quarterback prospects for the NFL draft is huge as well.”
The X-Pro technology is impacting Wilson’s own research and development as well. The data is actually teaching them about their own products and giving them insight into what design changes can be applied to make a better-performing football. As a supplier to major college programs with a wide product line, Wilson uses X-Pro-equipped balls for what they call ball fitting, the testing process teams use to decide which model of football they want to use. In the past, ball fitting was purely subjective. Football is still a traditionalist sport and some colleges pick their ball based on the color of the leather or the style of laces. The X-Pro data lets Wilson reps show coaches how their quarterbacks perform with different balls and make educated, analytical decisions.
X-Pro data has also confirmed what was long believed to be true, that a “broken-in” ball performs better than a brand new ball. NFL quarterbacks are notorious for the lengths they go through to get a ball the way they like it. They’ve been known to soak them in water, bury them in the ground, scuff them up with a stiff-bristle brush for hours upon hours, and even rub them with coffee grounds.
“There is a huge difference between the data of a broken-in ball and a new ball,” says Hare.
Ryan Ulrey, BS ’07, a manufacturing engineer at Wilson’s Ada factory, is an expert on breaking in footballs, or as he calls it, “putting a couple hours of love into it.” It’s just one of the many skills he’s developed over his 13 years at Wilson. Ulrey’s duties range from building manufacturing equipment, to improving manufacturing processes, to ball customization and creating all the stamping dies for the graphics that find their way onto NFL footballs. There is probably no better person in the world to help create a new leather football, which is why he played a key role in the development of Wilson’s flagship college and high-school game ball, the GST Prime.
The GST Prime isn’t constrained by 75 years of history like the Duke, so Wilson had free reign to design a revolutionary ball from the ground up.
“The NFL game ball hadn’t changed in any significant way in almost 80 years until we put the sensor in it,” says Ulrey. “But, we are trying to make a football that anybody can throw. The goal has always been to engineer a ball that holds a tight spiral no matter who throws it.”
To that end, Wilson incorporated additional stitching into the leather to provide more areas to grip the football. The GST Prime has more pronounced stitching on the stripes, and additional stitching on the ends of the ball and around the laces, meaning a quarterback with smaller hands, or one who has to throw the ball quickly (under three seconds) doesn’t have to catch the ball perfectly in order to grip it and throw it well.
All of their research told them that grip was key to throwing a football well. The balls are shipped with a protective coat of wax that makes the ball feel slick. When the wax is removed the balls become tackier to the touch. Since breaking in a ball is the key to grip, Wilson wanted a way to help consumers prepare their footballs so they perform at their best. They left the “how” to Ulrey. In fact, all decisions about how to manufacture a Wilson leather football are made by the team in Ada.
Ulrey used one of the machines he uses for imprinting graphics onto footballs to apply what Wilson calls the “prep gauge.” The process, known as ghosting, is typically used to apply shading to a custom graphic to give it depth. It darkens the leather the same way that scuffing up a ball with a stiff-bristle brush does. Ulrey realized that by ghosting a pattern on the ball, they could give consumers an idea of how long to scuff up their ball. When the prep gauge disappears, the ball is ready.
The GST Prime made its debut in NCAA football last fall in just three schools, one at each division. Wilson stuck with its hometown allegiances by selecting Ohio State University (Div. I), the University of Findlay (Div. II) and Ohio Northern University (Div. III) to test sensorless versions of the GST Prime. By all accounts, the balls were a hit. This spring, the OSU football program utilized the X-Pro technology in workouts, joining a who’s who of major college programs in adopting the technology.
The X-Pro is proving so popular that Wilson is having a hard time finding time to develop more use cases within the software.
“The X-Pro sensor is basically just a recording device, and it does a really good job of recording everything. There is so much data to sift through. Our software distills that information down to recognizable use cases related to throwing a football,” Hare says. “But there are far more use cases that we want to develop software for. The data is all there to do it.”
This fall, Ohio Northern is launching a new major in data analytics housed under the Center for Interdisciplinary Studies in the College of Arts & Sciences. The program, thanks to ONU’s favorite neighbor, is positioned to become an attractive destination for data analytics students due to its access to the X-Pro technology. Dr. Naeem Seliya, associate professor of computer science, is incorporating it in ECCS 2011-Introduction to Data Science beginning this fall. Seliya learned of the project from Springer and Ulrey at the Made in Ada Football Festival last August, and invited Hare to speak about it at an ONU Association of Computer Machinery (ACM) chapter meeting last fall. Last spring he advised then-junior Kenneth Eaton on an honors program project test-driving the technology for Wilson to see how well the data could be visualized and turned into useful information for ONU football coaches.
This year, Eaton and fellow senior Jordan Heitkamp will be using the X-Pro software for their senior capstone project. They are going to start the preliminary work on new use cases that Hare would love to see become part of the X-Pro software package. Specifically, the two computer science students will be looking through the data for meaningful metrics related to punting and kicking a football.
“This project will be a lot more hands-on than the one I did last semester because Wilson has not yet developed the technology for it. We will start with a list of raw numbers read out from the sensor itself and we will need to find a way for the system to determine what happened. For example, something in the data should tell us how far a kick went, or how much spin was on the ball and in what direction. That kind of information is important to the kicking game in football,” he says.
It’s kind of a dream come true for Eaton, a die-hard Kansas City Chiefs fan, who would love to work for a sports team someday. He knows that he’s involved at the leading edge of a growing area in data science, working with technology that is already an industry standard. In fact, his work this year will actively add to it by laying the foundation for a new use case.
“I see this as a way to really differentiate myself because very few computer science graduates will be able to say they have worked with this technology, let alone potentially designed a part of it. The combination of the unique experience and my career interests made this a perfect chance to develop practical skills and have a blast while doing it,” says Eaton.
Hare returned to ONU in May to upgrade the X-Pro system firmware with the latest version. When asked if any other college is using the X-Pro in their academic curriculum, he couldn’t think of any, and he is the person who would know. ONU has 12 X-Pro equipped GST Prime footballs that the Polar Bears will use in practices this upcoming season. That data will be analyzed and visualized by ONU students and provided back to ONU coaches, hopefully extending the competitive advantage of ONU and Wilson’s collaboration beyond the classroom and back onto the field where you might have expected it.